About us
iJility’s operation-driven programs increase productivity while our clients still maintain control of their operation.
Seasoned supply chain managers are engaged at the site level from implementation through the duration of the partnership. Resulting in reduced direct labor costs, higher efficiencies, AQLs, and a clear emphasis on safety.
Operation driven


Strategies that work
iJility specializes in Engineered Workforce Optimization programs. We use a highly refined labor management system to create a flexible workforce that includes our Process Integrity Programs (PIP) to align with our client’s AQL standards.
iJility’s solutions are comprised of our workforce, management team, training, quality, safety, W/C accountability, and OSHA Log administration.
Innovative results
Case Studies
Real results...proof that iJilityWINs for our clients.
Your success.
Case study... how iJilityWINs for our clients
E-commerce
iJilityWORX Discovery
The organization moved its facility across state lines, hired new leadership, had no tribal knowledge, and lacked operational processes. Some brands had an inbound receipt backlog of 3+ mos. Returns had a six-month backlog. Fill accuracy, pick & pack efficiencies, and cost per order were severely underperforming, the facility was almost at a gridlock state.
iJilityPATH to Success
-
Created an iJility Task Force Engagement Team
Engineers - Operations - Recruiting
-
Remap Facility
-
Streamline DTS
Consolidated footprint of 65K+ SKUs for 6 major brands
-
Returns required relocation to offsite facility
Located/Opened/Began operations
-
Sourcing & Management of 150+ employees
iJilityIMPACT
Results
45.6%
PICKING EFFICIENCY
46.6%
14.97%
PACKING EFFICIENCY
DTS ACCURACY
53.3%
OVERALL FULFILLMENT
COST PER ORDER
29%
DTS DAMAGE RATE
40.6%
DTS COST PER ORDER
36%
RETURNS PROCESSING COSTS
71%
Processing /Packing UPH Increased
iJilityIMPACT
Results
9.9%
ORDER ACCURACY
38%
OUTPUT
30%
VOLUME ORDER INCREASE
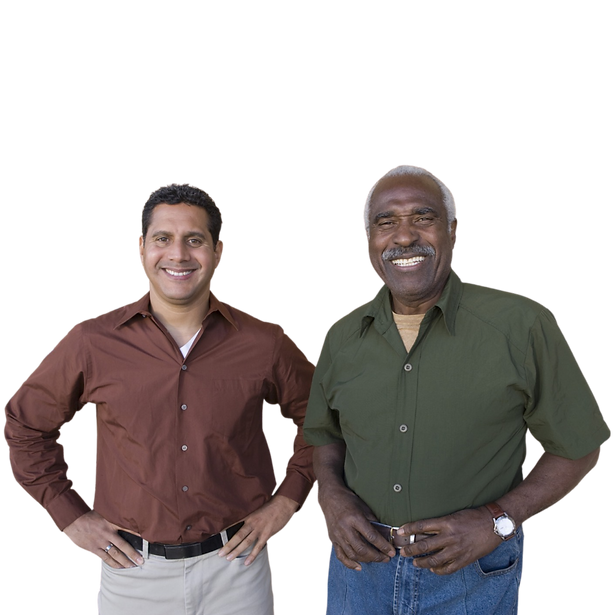
22%
OVERALL FULFILLMENT COST PER UNIT
71%
Processing /Packing UPH Increased
Distribution
iJilityWORX Discovery
The organization operated with 100% full-time employees and was experiencing huge growth. Poor employee performance, high turnover, difficult labor market, pandemic, and low productivity created culture erosion. Lack of employee teamwork and accountability were increasing; employees refused to work overtime required to meet volume demands. The site was struggling with quality levels, lack of cross-training programs, and increased costs.
Phase 1 Goal: Workforce Stabilization
iJilityPATH to Success
-
Integration of iJility Engagement team
Focused -developed and enforced a "Culture of Success"
-
Communicated and implemented workforce expectations
Flexibility -Cross-Training - Labor Sharing
-
Monitored performance and provide feedback to ensure accountability
Phase 2 Goal: Operational Enhancements
-
Integrated additional resource - Regional Manager
-
Implemented PIP – Process Integrity Programs
Standardized quality & training program
Developed and implemented process integrity audits
Completed product references for kitting
-
Enhanced workflow-reduced kitting changeover times
-
Implemented production & quality tracking, analysis, and employee feedback process
-
Implemented root cause analysis process
-
Enhanced departmental communication
Standard daily performance reports to client
Skills matrix by employee and job function
